Welcome to the self-guided tour of la Papeterie Saint-Gilles !
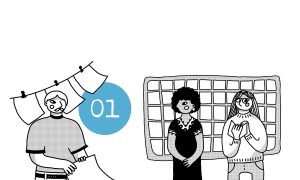
What is the Artisans at work experience?
La papeterie Saint-Gilles was the first economuseum, inaugurated in 1988, 23 years after its foundation. Today, this network includes: 50 organizations in Quebec, 25 in Canada and 48 internationally.
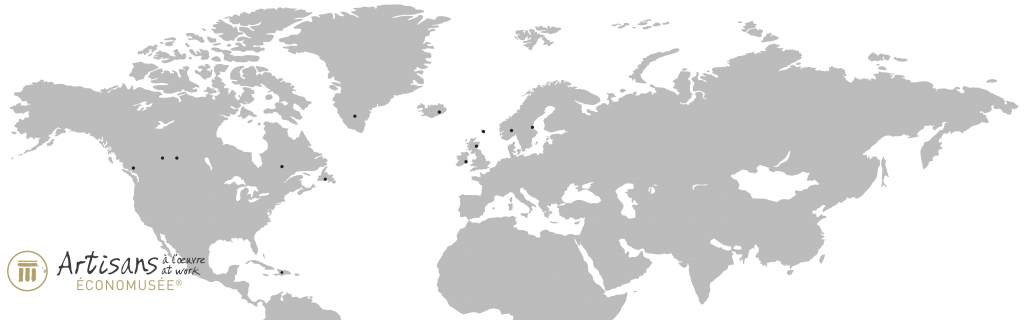
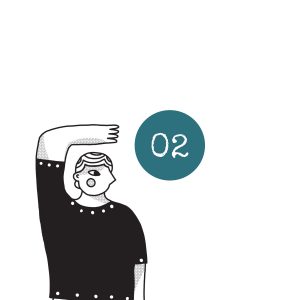
A papermill, four anchors
Mgr. Félix-Antoine Savard, the founder. Captivated by artisanal work which he perceived to be of sociocultural value and a lever for the region’s economy, Mgr. Savard decided to start a paper making operation to honor the writer as well as the paper maker.
Marc Donohue, the patron. A long-time friend of Mgr. Savard and president and managing director of the Donohue Papermill in Clermont, today known as Résolu Forestry Products. For several years, Mr. Donohue provided financial support to the Papeterie.
Georges Audet, the papermaker. Trained in the United-States and in France, the skillful boat craftsman, who had a great sense of humor, was the first papermaker hired by the Papeterie.
Cyril Simard, the visionary. Close friend of Mgr. Savard and chosen to become his successor, the architect and ethnoscientist decided to advance his concept for an economuseum to link culture and economy. Thus, in 1988, the Papeterie Saint-Gilles becomes the first economuseum.
In order of appearance: Georges Audet, Bishop Félix-Antoine Savard and Cyril Simard.
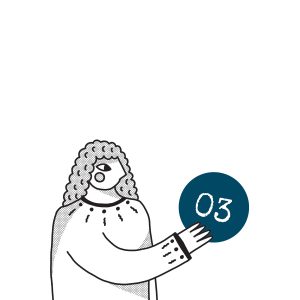
How did the Papeterie take the Saint-Gilles name?
Two reasons are given for the Papeterie’s name. First, it was chosen to honor the spouse of Marc Donohue’s uncle, Alice Béant de Saint-Gilles who ran a farm known as the Saint-Gilles farm in La Malbaie. Second, because Mgr. Savard liked the Saint-Gilles legend; a wandering christian monk who became the patron saint of infirms, beggars and blacksmiths.
Anecdotally, Mgr. Savard was often heard to say that Saint Gilles had made a vow to seek and honor beauty and that became the slogan of the Papeterie!
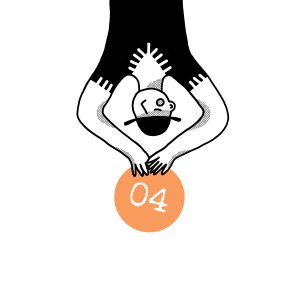
The village school
The Papeterie Saint-Gilles was located in the old schoolhouse in Saint-Joseph-de-la-Rive. Built in 1901, the building welcomed children from the first six years of primary school. The first schoolmistresses, as they were then known, were Yvette Tremblay, of Baie-Saint-Paul and Laurette Tremblay, from Les Éboulements. The Papeterie took over the building when the school closed in 1964. At first, the mill rented the space but in 1975, the Papeterie bought the building for $1,000.
The small row school, in 1934

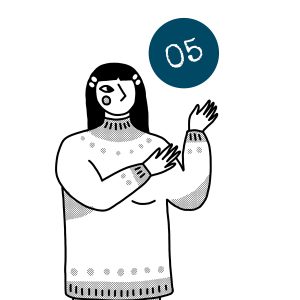
Six steps for producing handmade paper
1. Shredding
The first step is the preparation of the pulp. First, cotton linters are coarsely shredded by hand and then transferred to the defibration Hollander pile; the pile acts as a big mixer and in a little while, our paper pulp is ready. We then add a small amount of glue to offset the blotter effect.
2. Steeping and screening
Then we pour the paper pulp in a beater tub. To make a paper sheet, we need a deckle and a frame: the frame is a screen made up of brass wire attached to wooden rods. The deckle is a mobile cover that fits on the frame and is used to set the sheet format. The paper maker dips this in the beater tub and brings it up full of paper pulp, shaking it in back and forth to let the water drain.
3. Coating the sheet
Once the sheet has settled on the surface of the screen, it must be taken off its support. The removal of the sheet consists in turning over the screen on a surface of wool felt to remove it from its support. The water-logged sheets are then spread out between felts. We end up with a pile of 100 sheets called a pack.
4. Pressing
The sheets interleaved in the felts are pressurized to eliminate as much water as possible. We use a hydraulic press generating about 30 tons.
5. Drying
The damp sheets are taken to the drying room and spread out one by one on a dryer. Drying takes about 24 hours in a room where humidity is controlled.
6. Calendering
The last step consists of smoothing out the sheets because during the drying period, sheets retract and warp. To obtain a smooth effect, we put the sheets in a calender to be levelled evenly by two huge steel drums. Then, the paper sheets are ready for use. We save several sheets that have not gone through this process for those who prefer a textured paper sheet.
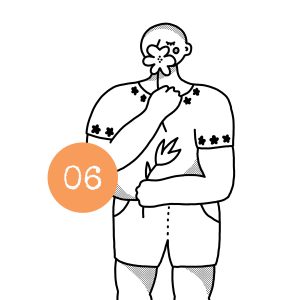
A hint of flowers
Saint-Gilles paper is known for the presence of locally grown flowers in its composition. Before being added to the pulp, the flowers are treated in a secret recipe!
Purple loosestrife: a large perennial reaching 1 to 1,5 meters high. Its vibrant purple flowers are greatly loved for their esthetic qualities.
Sweetgrass: perennial reaching a height of 30 to 80 cm. Flowers range from yellow to orange according to the variety.
Sedge Warblier: perennial also called common reed. reaching up from 3 to 5 meters. Flowers come in the shape of feathers. This plant is abundant, even outcompeting other plants… and the Papeterie has found a use for it!
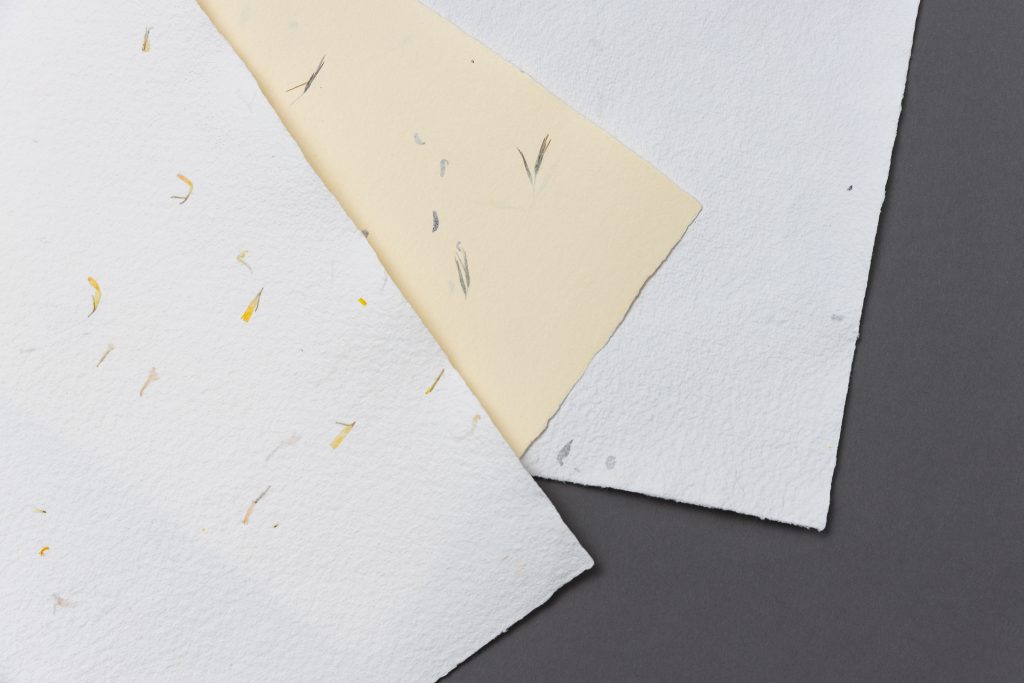
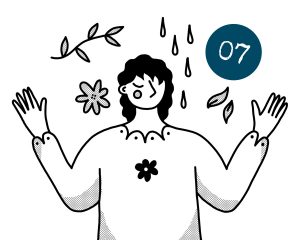
Natural and…
Saint-Gilles paper is made from 100% cotton fibers. Too short to be woven, these fibers are ideal for the manufacture of paper.
… Eco-friendly
Saint-Gilles paper does not come from felled trees nor uses bleaching agents during its manufacturing process. Besides which, the Papeterie also gives a second life to fibers since these are too short to be of any use to the textile industry.
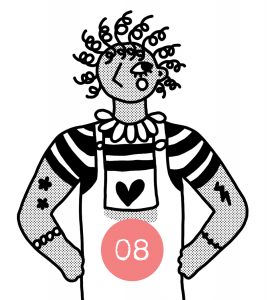
Unique and inimitable!
Saint-Gilles paper has an impeccable reputation for purity, durability, flexibility, tolerance and stability. Moreover, the paper is lignite-free, a photosensitive molecule responsible for the yellowing of paper when it is exposed to light. The Saint-Gilles watermark is inlaid in each sheet making our paper a unique and inimitable product.
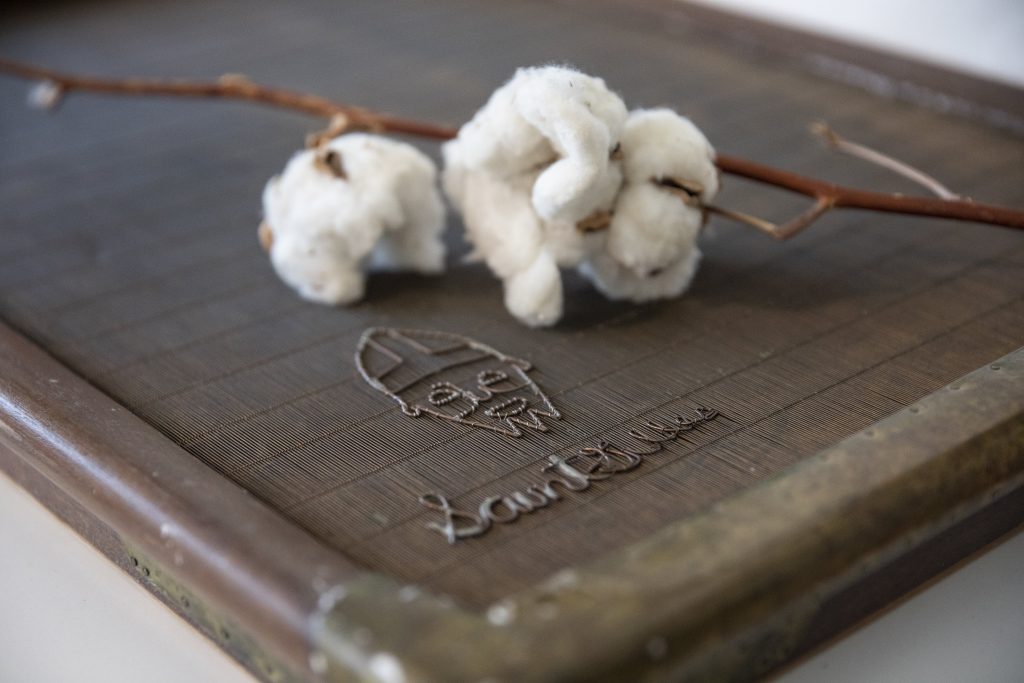
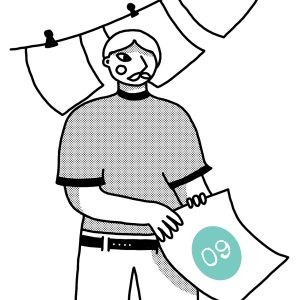
Zoom on fibers
A thirsty paper!
It seems that blotter paper was invented by mistake. During manufacturing operations, an error in dosage created a porous, thicker paper. Quickly, the porous property of the paper allowed it to absorb small quantities of liquids, notably ink. The capillarity effect was responsible for this. This is the reason why it was used extensively over the years as a sheet, a desk blotter pad and also to cover blotters used to sop up ink.
The strange kind of paper!
Paper is made from trees, right?
Not necessarily. In fact, any kind of fibrous material can be used to make paper. Bamboo, the bark of the mulberry tree, sugar cane and even, would you believe, elephant droppings! In olden times, paper was made with clothing and recycled rags.
The great industrial papermills make their paper from wood whereas the Papeterie Saint-Gilles makes it paper from cotton.
Compared to wood, cotton needs little transformation. It comes from a small white flower growing on a stem, whereas wood…that’s an entire tree!
Long fiber, short fiber
Fiber length plays a determining role in papermaking operations. To start, we will take a look at cotton fibers.
Cotton fibers are extracted from the cotton flowers and are spunned to produce fabrics. But after this operation, there is still a certain amount of cotton left.
Leftover cotton strands are pressed together in the shape of large sheets known as “cotton linters” or lint. Their appearance is akin to the moss found in the dryer filter.
Lint is then sent to papermills where it is transformed and mixed with wood pulp.
Here at the Papeterie, all the cotton fibers enter in the manufacture of paper pulp.
A pencil made to measure!
The writing implement associated with papyrus and clay tablets is a pen cut and sharpened from a reed. Since writing flows from left to right, the reed pen is cut at an angle to facilitate this particular type of writing.
A well-garnished pencil box!
Over the centuries, several implements were used to write. Among the oldest ones, we find the goose feather, the reed pen and the paintbrush. In the middle of the 19th century, we find a steel-nib pen so followed by the fountain pen. The ballpoint pen arrived on the scene in the 1940’s.
Lead has a bad reputation!
Our good old lead pencil was invented in the 18th century. Manufactured with a graphite base, it does not contain one single iota of lead! Then why give it such a name? First, because during the Middle Ages, writers used a sharpened piece of lead and, second, when graphite was discovered in the 16th century, this pure black mineral was given the name « plumbagin ».
Click on the images to learn about the ingredients used to make these papers.

Sizing or gluing
What is sizing or gluing?
An additive is added either to the pulp (internal sizing) or to the dried sheet (external or surface sizing) to waterproof the sheet of paper. Without this precaution, ink would flow through the fibers and expand,
The importance of sizing or gluing
Generally, when you choose a writing paper, you’ll want to obtain a neat stroke and especially avoid letting ink go through the paper sheet. So, paper needs to have a certain amount of resistance to water and that resistance is obtained by sizing or gluing.
Microscope images: ink on paper
- Printer paper: made to absorb ink droplets from the printer. You can see that the ink is absorbed by the paper and that the stroke is enlarged and fused into the fiber. This paper is not suited for writing with ink.
- Papier for ink pens: made to take a longer time to dry so that the stroke will remain neat and tidy. Moreover, even if the sheet is thin, ink does not go through on the other side of the sheet.
So, what kind of sizing or gluing is used?
Throughout history, several substances were used to waterproof paper; starch as that found in potatoes, or wheat gluten. However, these processes made paper more susceptible to be eaten by vermin.
The first industrial papers were treated with rosin and alum. This caused a great amount of PH loss in paper and what followed was premature yellowing. Today, wax or oil-based synthetic sizing are commonly used. This gives us a more stable paper, resistant to insects and yellowing.
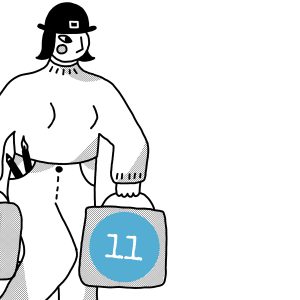
The history of fibers and notable inventions
Well before our printer paper, humans used several handy materials to write. Certain inventions, inextricably linked to the history of paper, have revolutionized our rapport to writing and communications.
Pre-historic times: writing on stone, bone, wood, bronze and clay.
-5000: emergence of papyrus in Egypt. Made from the Nile reed, papyrus is the origin of the word « paper ».
2nd century AA: invention of parchment paper in Pergame (Turkey) made from lamb, kid or veal skins.
Year 105: in China, Cai Lun codifies the art of manufacturing paper from « bark, hemp, rags and fishing nets». However, latter archeological discoveries have shown an earlier usage of paper going back to two centuries.
8th century: the art of paper making is introduced to Japan and from then, step by step, to Western countries by the Arabs.
12th century to the middle of the 19th century: flax, hemp and cotton rags are used to manufacture paper.
1455: In Mayence (Germany), Johann Gutenberg invents the press as we know it today (mass production), to develop a typographical process of moveable characters but the Chinese and Koreans had invented the press many hundreds of years previously.
1673: Invention of the Holland cylinder, or Holland beater, a type of tank with shredding blades in its center to shred rags.
1799: Invention by Louis-Nicolas Robert of the first continuous paper machine.
Years 1840: Development of the first mechanical wood pulp.
Years 1860: Introduction of chemical pulp, combining wood chips and chemical products.
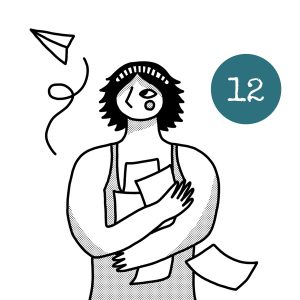
A surprising journey!
To start with, paper is linked to a sheet used for writing and drawing. But throughout the course of its history, paper has known extraordinary uses! Even today, paper is not done with us!
Strangely enough, the advent of digital times has seen an increase in our paper consumption: each order at Amazon (or others!) generates tons of cardboard and wrapping paper.
The structuring paper (top hat)
Before the use of plastic or other contemporary materials, paper was present as a structuring element in all kinds of situations: hats, handbags, suitcases and many other uses.
Armored Paper
The Ancient Chinese made an admirable use of paper and not only for painting and calligraphy. In fact, they used paper armor and this type of armor revealed itself to be as reliable, durable and efficient as their metal equivalents. Use of paper armor goes back to 600 AA; the paper was coated with a special resin or shellac to render it waterproof and more compact. The onset of guns brought this type of protection to an end, as well as its steel counterpart in the 19 th century.
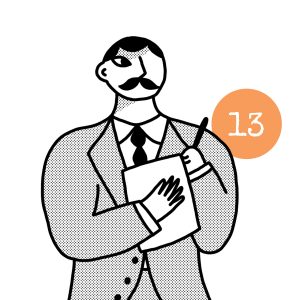
The Donohue plant: a Charlevoix industry
In 1911, a mechanical pulp plant was erected at Chute Nairne, now the city of Clermont. After difficult beginnings, the company belonging to the brothers Timothée and Charles Donohue enjoyed a rapid and strong growth. At the height of its success, in the 70’s, the company had a roster of nearly 1 000 people: 620 in the plant and more than 350 in the forest.
The company became Résolu Forestry Products in 2011 and is linked to the history of Clermont. In fact, the company has contributed to the promotion of the Town of Clermont in 1935.
Over the years, the company involved itself heavily in the various aspects of the life of the community, in city councils, school boards and chambers of commerce while never forgetting the role it played in the creation of the Papeterie Saint-Gilles.
Here are some images of the log drive and paper mills in the 19th century.
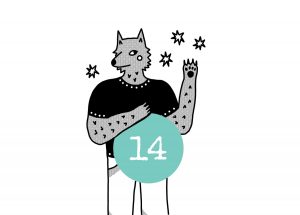
A country of myths and story tellers!
Lots of stories were told and retold in Charlevoix starring Satan, religion, strong men or tearful lovers. This artform was favored by the forestry companies who hired story tellers to amuse and entertain the woodcutters working in their camps. Read up on La chasse-galerie, Alexis le trotteur, La roche pleureuse, La noyée de Charlevoix and l’Hercule du Nord.
Charlevoix legends, myths, gossip, are all called a chouenne!
Paper allows us to preserve all such stories, transmitted for generations, by word of mouth…
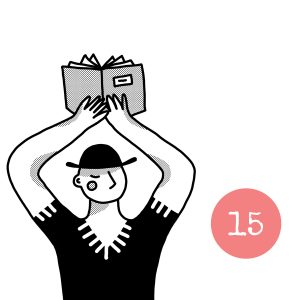
Bookbinding: discover this art
Artisanal bookbinding is still in practice today. This art needs patience, rigor and a meticulous attention to details.
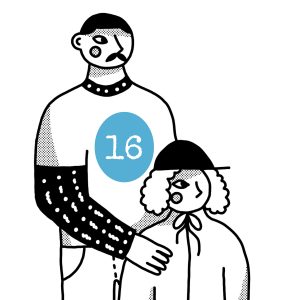
Hot or cold pressing?
Whether the pressing is done either in heat or cold conditions, both have a direct influence on the texture of the paper. The choice will be made according to the type of paper sought after.
Paper pressed under heat go through heating rollers which give a smooth textured paper. Printer paper and most commercial papers nowadays are the result of this method.
Paper that is cold rolled undergoes the same treatment but without the heat. Consequently, the paper will have a more substantial texture. Watercolor paper and Saint-Gilles papers are pressed by this method.
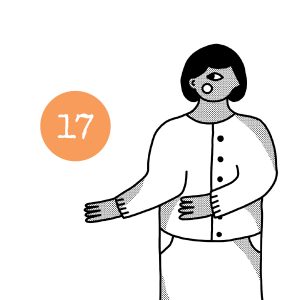
Are the sheets dried?
After pressing, sheets are laid out, one by one, on a dryer. The drying period lasts about 24 hours.
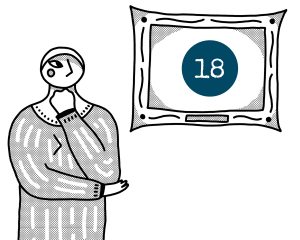
A collection for the ages!
What do Quebec painters Claude Le Sauteur, Jean-Paul Lemieux, Alfred Pellan or Marc-Aurèle Fortin have in common? These renowned artists and many others have participated annually in the plan to offer a limited-edition silk-screen rendition of one of their artworks. This fund-raising activity is at the heart of the rich collection of the Papeterie Saint-Gilles.
Silk-screen printing, giclée, lithography… an explanation!
Silk-screen printing is a process done on a synthetic silk screen stretched on a wood or aluminum frame. Works chosen for this process will undergo color separation, which consists in the production of four computer files for each of the primary colors, i.e., blue, red and yellow as well as black; four different films will be prepared. Printing is done with a scraper that helps the silk absorb the ink. Beforehand, the silk has been submitted to each color separation by a photographic process.
To give depth to the images, reproductions of the Papeterie Saint-Gilles, made by the master silk-screen printer André Lemieux, can amount to 40 color passes generally. So, for a run of 150 copies, 6000 ink passes with the scraper will have been necessary.
The term giclée designates the impression of a large format artwork on a high-definition ink jet printer. There are no limits to the number of impressions that can made and several support media can be used: paper, canvas, etc.
Lithography, litho or photolithography in general refers to mass production done by a commercial printing house. Engraving on stone or metal necessitates that the artist or the craftsman go through many steps and a hand-made impression.
image of a color separation (4 colors) + final work: black, yellow, magenta and cyan (CMYK).
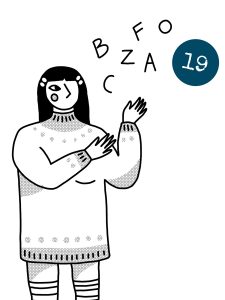
A vocabulary specific to our industry
Capillarity: a phenomenon explaining the capacity of water and of certain liquids to naturally rise despite gravitational forces. One can see the phenomenon in action when a blotter draws up ink or when ink permeates the paper on which one writes.
Calendar: a machine constituted of cylinders and rollers, used to smoothe out paper.
Chain lines: a grid composed of brass wires to form a metallic backdrop to retain the pulp. Marks left by these chain lines give the paper its name, i.e., « laid paper ».
Grammage: a term used to describe the weight of a sheet of paper with a surface of one square meter. If a sheet is thick, it has more weight. A printer paper sheet weighs about 80 grams. Therefore, an 80-gram sheet of paper is in fact one square meter, weighing 80 grams
Laid Paper: paper sufficiently transparent to show fine parallel lines horizontally in the depth of the paper.
Lignin: one of the main components of wood, second in importance to cellulose. Since this component is highly photosensitive, it contributes greatly to the yellowing of paper.
Linters: short fibers that remain stuck on the seeds of certain cotton plants after deseeding. It is also the name of the cotton sheets entering in the manufacture of Saint-Gilles paper.
Paper stack: a pile of paper sheets removed from the felt pads, immediately after pressing. The sheets will then be dried.
Porse: a pile of 100 waterlogged sheets inserted between the felt pads.Rags: clothing and various types of linen made from plant fibers, mainly flax and hemp, used into the manufacturing of paper.
Rag-picker: people in charge of picking up old and used clothes, known as rags and bringing them to papermills.
Saint-Gilles Beard: the fringe found on the four sides of Saint-Gilles paper.
Shredder or Holland beater: the machine that shreds cotton fibers into a pulp that is ready to manufacture paper, after dilution of the pulp.
Table rolls: wood or metal rods binding both sides of the framework and supporting the finer and tighter-woven brass wires, the vergeures or chainlines, making up the bottom of the framework, in a perpendicularly pattern.
Torchon or rag: an uncalendered sheet, i.e., unpressed. Highly textured sheets with a coarse structure are often highly prized by artists.
Vellum: the skin of a stillborn veal calf, finer than ordinary parchment paper.
Watermark: a drawing printed in the paper thickness. It can be seen by transparence. Once upon a time, it was a document’s guarantee of authenticity and is still used today, with paper money, for example.
Thank you for your visit
Let’s participate !
Participate in the revitalization of this heritage site by contributing to our fundraising campaign.